1. Theoretische test en analyse
Van de 3ventielen van bandenmonsters geleverd door het bedrijf, 2 zijn kleppen en 1 is een klep die nog niet is gebruikt.Voor A en B is de klep die niet is gebruikt grijs gemarkeerd.Uitgebreide afbeelding 1. Het buitenoppervlak van klep A is ondiep, het buitenoppervlak van klep B is het oppervlak, het buitenoppervlak van klep C is het oppervlak en het buitenoppervlak van klep C is het oppervlak.Kleppen A en B zijn bedekt met corrosieproducten.De klep A en B zijn gebarsten in de bochten, het buitenste deel van de bocht bevindt zich langs de klep, de klepringmond B is naar het uiteinde gebarsten en de witte pijl tussen de gebarsten oppervlakken op het oppervlak van klep A is gemarkeerd .Uit het bovenstaande blijkt dat de scheuren overal zijn, de scheuren zijn het grootst en de scheuren zijn overal.
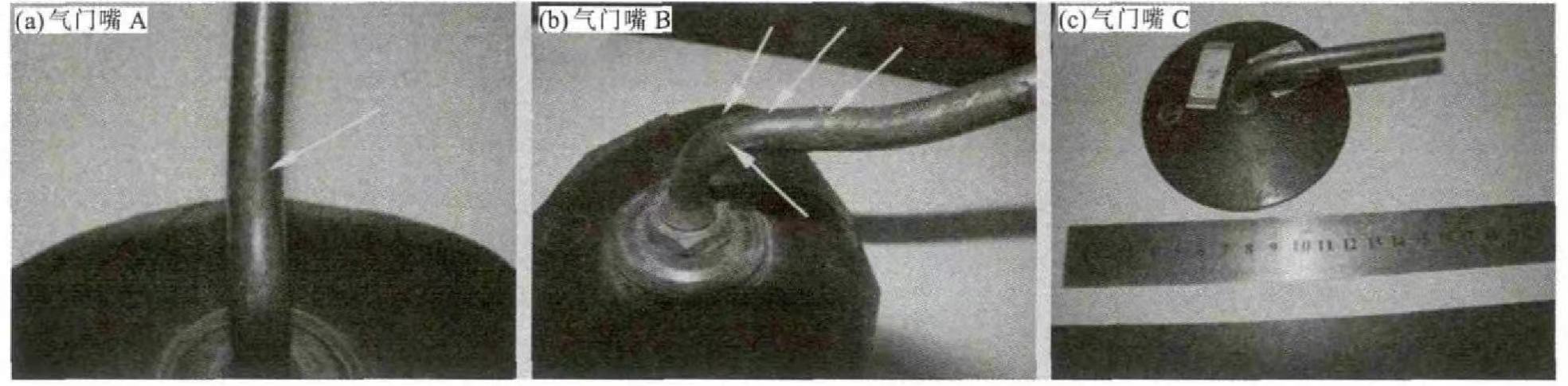
Een gedeelte van debandventielA-, B- en C-monsters werden uit de bocht gesneden en de oppervlaktemorfologie werd waargenomen met een ZEISS-SUPRA55 scanning-elektronenmicroscoop, en de samenstelling van het microgebied werd geanalyseerd met EDS.Figuur 2 (a) toont de microstructuur van het oppervlak van klep B.Het is te zien dat er veel witte en heldere deeltjes op het oppervlak zijn (aangegeven door de witte pijlen in de figuur), en de EDS-analyse van de witte deeltjes heeft een hoog gehalte aan S. De resultaten van de energiespectrumanalyse van de witte deeltjes worden getoond in Figuur 2(b).
Figuren 2 (c) en (e) zijn de oppervlaktemicrostructuren van klep B. Uit figuur 2 (c) blijkt dat het oppervlak bijna volledig bedekt is door corrosieproducten, en de corrosieve elementen van de corrosieproducten door energiespectrumanalyse omvatten voornamelijk S, Cl en O, het gehalte aan S in individuele posities is hoger en de resultaten van de energiespectrumanalyse worden getoond in figuur 2 (d).Uit figuur 2(e) blijkt dat er microscheurtjes zijn langs de klepring op het oppervlak van klep A. Figuren 2(f) en (g) zijn de micromorfologieën van het oppervlak van klep C; het oppervlak is ook volledig bedekt door corrosieproducten, en de corrosieve elementen omvatten ook S, Cl en O, vergelijkbaar met figuur 2(e).De reden voor scheuren kan spanningscorrosiescheuren (SCC) zijn, afkomstig van de corrosieproductanalyse op het klepoppervlak.Fig. 2(h) is ook de microstructuur van het oppervlak van klep C. Het is te zien dat het oppervlak relatief schoon is en dat de chemische samenstelling van het oppervlak, geanalyseerd door EDS, vergelijkbaar is met die van de koperlegering, wat aangeeft dat de klep niet gecorrodeerd.Door de microscopische morfologie en chemische samenstelling van de drie klepoppervlakken te vergelijken, wordt aangetoond dat er corrosieve media zoals S, O en Cl in de omgeving voorkomen.
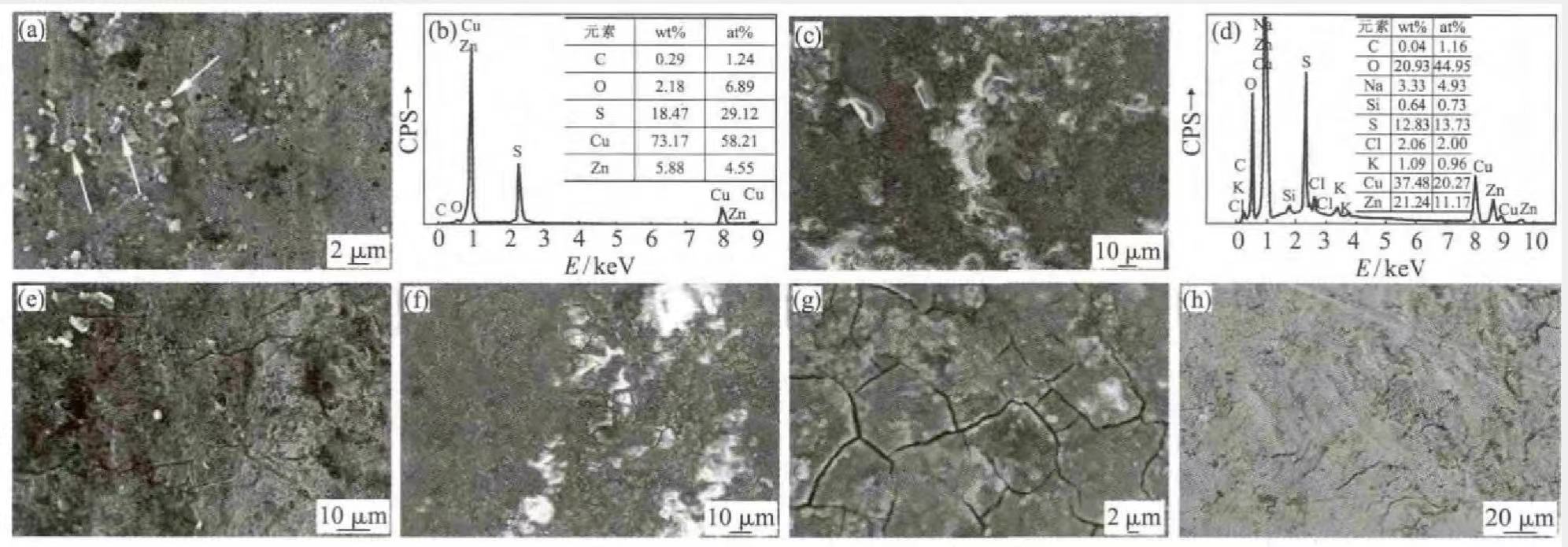
De scheur van klep B werd tijdens de buigtest geopend en er werd vastgesteld dat de scheur niet door de gehele dwarsdoorsnede van de klep drong, scheurde aan de zijkant van de achterwaartse bocht en niet barstte aan de zijde tegenover de achterwaartse bocht. van de klep.Uit de visuele inspectie van de breuk blijkt dat de kleur van de breuk donker is, wat aangeeft dat de breuk gecorrodeerd is, en dat sommige delen van de breuk donker van kleur zijn, wat aangeeft dat de corrosie op deze delen ernstiger is.De breuk van klep B werd waargenomen onder een scanning-elektronenmicroscoop, zoals weergegeven in figuur 3. Figuur 3 (a) toont het macroscopische uiterlijk van de breuk van klep B.Het is te zien dat de buitenste breuk nabij de klep bedekt is door corrosieproducten, wat opnieuw wijst op de aanwezigheid van corrosieve media in de omgeving.Volgens energiespectrumanalyse zijn de chemische componenten van het corrosieproduct voornamelijk S, Cl en O, en zijn de gehalten aan S en O relatief hoog, zoals weergegeven in figuur 3 (b).Bij het observeren van het breukoppervlak blijkt dat het scheurgroeipatroon langs het kristaltype verloopt.Een groot aantal secundaire scheuren kan ook worden gezien door de breuk bij hogere vergrotingen te observeren, zoals weergegeven in figuur 3(c).De secundaire scheuren zijn in de figuur gemarkeerd met witte pijlen.Corrosieproducten en scheurgroeipatronen op het breukoppervlak vertonen opnieuw de kenmerken van spanningscorrosie.
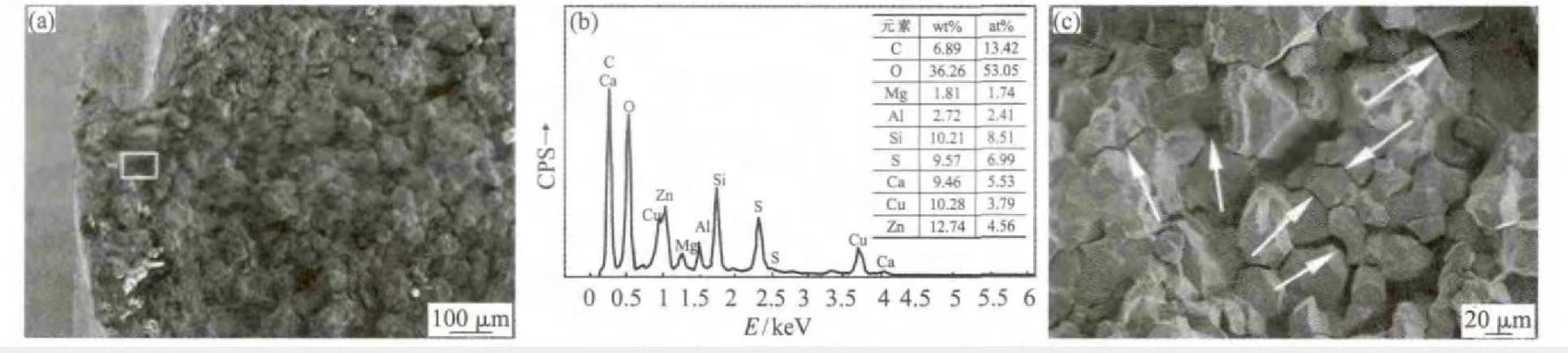
De breuk van klep A is niet geopend, verwijder een deel van de klep (inclusief de gebarsten positie), slijp en polijst het axiale gedeelte van de klep en gebruik Fe Cl3 (5 g) +HCl (50 ml) + C2H5OH ( 100 ml) oplossing werd geëtst en de metallografische structuur en scheurgroeimorfologie werden waargenomen met de Zeiss Axio Observer A1m optische microscoop.Figuur 4 (a) toont de metallografische structuur van de klep, die een α+β tweefasige structuur is, en β relatief fijn en korrelig is en verdeeld over de α-fasematrix.De scheurvoortplantingspatronen bij de omtreksscheuren worden getoond in figuur 4(a), (b).Omdat de scheuroppervlakken gevuld zijn met corrosieproducten, is de opening tussen de twee scheuroppervlakken groot en is het moeilijk om de scheurvoortplantingspatronen te onderscheiden.bifurcatie fenomeen.Er werden ook veel secundaire scheuren (gemarkeerd met witte pijlen in de figuur) waargenomen in deze primaire scheur, zie figuur 4 (c), en deze secundaire scheuren plantten zich voort langs de korrel.Het geëtste klepmonster werd door SEM geobserveerd en er werd vastgesteld dat er veel microscheurtjes waren op andere posities evenwijdig aan de hoofdscheur.Deze microscheurtjes ontstonden vanaf het oppervlak en breidden zich uit naar de binnenkant van de klep.De scheuren hadden een vertakking en strekten zich uit langs de korrel, zie figuur 4 (c), (d).De omgevings- en spanningstoestand van deze microscheuren zijn bijna dezelfde als die van de hoofdscheur, dus kan worden geconcludeerd dat de voortplantingsvorm van de hoofdscheur ook intergranulair is, wat ook wordt bevestigd door de breukobservatie van klep B. Het bifurcatiefenomeen van de scheur vertoont opnieuw de kenmerken van spanningscorrosie van de klep.
2. Analyse en discussie
Samenvattend kan worden geconcludeerd dat de schade aan de klep wordt veroorzaakt door spanningscorrosiescheuren veroorzaakt door SO2.Spanningscorrosiescheuren moeten doorgaans aan drie voorwaarden voldoen: (1) materialen die gevoelig zijn voor spanningscorrosie;(2) corrosief medium dat gevoelig is voor koperlegeringen;(3) bepaalde stressomstandigheden.
Algemeen wordt aangenomen dat zuivere metalen geen last hebben van spanningscorrosie, en dat alle legeringen in verschillende mate gevoelig zijn voor spanningscorrosie.Voor messingmaterialen wordt algemeen aangenomen dat de tweefasige structuur een grotere gevoeligheid voor spanningscorrosie heeft dan de enkelfasige structuur.In de literatuur is gerapporteerd dat wanneer het Zn-gehalte in het messingmateriaal 20% overschrijdt, het een hogere spanningscorrosiegevoeligheid heeft, en hoe hoger het Zn-gehalte, hoe hoger de spanningscorrosiegevoeligheid.De metallografische structuur van het gasmondstuk is in dit geval een α+β tweefasige legering en het Zn-gehalte is ongeveer 35%, ruim boven de 20%, dus het heeft een hoge spanningscorrosiegevoeligheid en voldoet aan de materiële voorwaarden die vereist zijn voor spanning corrosie scheuren.
Als bij messingmaterialen het spanningsontlaten niet wordt uitgevoerd na vervorming bij koud bewerken, zal spanningscorrosie optreden onder geschikte spanningsomstandigheden en corrosieve omgevingen.De spanning die spanningscorrosiescheuren veroorzaakt, is over het algemeen lokale trekspanning, die uitgeoefende spanning of restspanning kan zijn.Nadat de vrachtwagenband is opgepompt, zal er door de hoge druk in de band trekspanning worden gegenereerd in de axiale richting van het luchtmondstuk, waardoor er scheuren in het luchtmondstuk aan de omtrek zullen ontstaan.De trekspanning veroorzaakt door de interne druk van de band kan eenvoudig worden berekend volgens σ=p R/2t (waarbij p de interne druk van de band is, R de binnendiameter van het ventiel en t de wanddikte van de band). de klep).Over het algemeen is de trekspanning die wordt gegenereerd door de interne druk van de band echter niet te groot en moet rekening worden gehouden met het effect van restspanning.De kraakposities van de gasmondstukken bevinden zich allemaal bij de achterwaartse buiging, en het is duidelijk dat de resterende vervorming bij de achterwaartse buiging groot is en dat daar een resterende trekspanning aanwezig is.In veel praktische componenten van koperlegeringen worden spanningscorrosiescheuren zelden veroorzaakt door ontwerpspanningen, en de meeste worden veroorzaakt door restspanningen die niet worden opgemerkt en genegeerd.In dit geval is bij de achterste bocht van het ventiel de richting van de trekspanning die wordt gegenereerd door de interne druk van de band consistent met de richting van de restspanning, en de superpositie van deze twee spanningen levert de spanningsconditie op voor de SCC .
3. Conclusie en suggesties
Conclusie:
Het kraken van debandventielwordt voornamelijk veroorzaakt door spanningscorrosie, veroorzaakt door SO2.
Suggestie
(1) Traceer de bron van het corrosieve medium in de omgeving rond debandventielen probeer direct contact met het omringende corrosieve medium te vermijden.Op het oppervlak van de klep kan bijvoorbeeld een laag anticorrosiecoating worden aangebracht.
(2) De resterende trekspanning bij koudvervormen kan worden geëlimineerd door geschikte processen, zoals spanningsvrij gloeien na buigen.
Posttijd: 23 september 2022